The SIPOC model helps an organization document processes at a high-level. Each process is documented in its own unique SIPOC document as a table. This makes it easy to understand the critical elements of each process at a glance.
Imagine you work for a large organization and have been asked to lead a team to improve some complex processes. Where would you start? Your first step might be to get a better understanding of the current processes.
This is precisely what SIPOC (pronounced sigh-pock) can help you to do. If you already had SIPOC documents in place for your processes, then for each process, you’d be able to answer some really important high-level questions at the beginning of a project:
- What is the scope? That is, where does the process begin and end.
- Who are the stakeholders? That is, who are the suppliers and customers.
- What should we be measuring? That is, what are the key steps of the process and the inputs and outputs.
The SIPOC Model
When you first glance at the SIPOC diagram below, you’d be forgiven for thinking that SIPOC is a complex tool to understand and use. It isn’t. It is actually a very simple way to get an overview of a process in a table format.
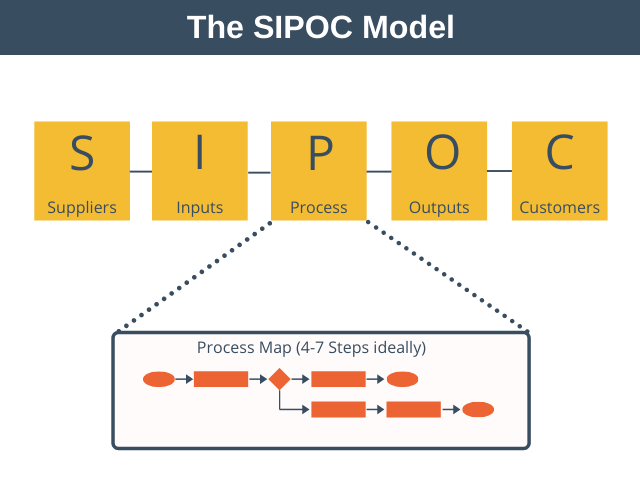
SIPOC is an acronym standing for Suppliers, Inputs, Process, Outputs, and Customers. The SIPOC model provides a way to understand the key elements that interact with a process and the process itself.
Background
SIPOC diagrams originated in the 1980s as a part of Total Quality Management (TQM). TQM focuses on ensuring quality through adherence to standards. SIPOC is also used these days as part of Six-Sigma. Six-Sigma is different from TQM as it concentrates on improving quality by removing the number of defects.
SIPOC diagrams are most commonly used during the define phase of a DMAIC (Define, Measure, Analyze, Improve, Control) process in Six Sigma.
When to use SIPOC?
To maintain competitiveness in today’s world, organizations need to continually adapt and improve. In practice, this will mean updating and improving complex processes. If you simply jump in and start changing a complex process, you may encounter unintended negative consequences. By first using SIPOC to have a baseline understanding of the processes you want to change, you make it far more likely for your change to be successful and avoid unintended consequences.
Broadly speaking, there are three groups of people who can benefit from using SIPOC:
- Those new to a process who need to get a quick overview of it.
- Those familiar with a process but who need to be brought back up to speed for whatever reason. Perhaps the process has changed in some way since they last considered it.
- Those looking to improve or change a process in some way.
The SIPOC Model Parts
A SIPOC table consists of five parts. Let’s take a brief look at each of them.
1. Process
The most important part of a SIPOC diagram is the process it is based on. A process is a set of activities that take one or more inputs from one or more suppliers and turns them into one or more outputs used by one or more customers.
Your aim in the SIPOC process section is to describe or draw the process at a high-level using just 4 to 7 steps. Limiting the number of process steps forces you and your team to zoom out from the detail and consider the big-picture.
If you find you’ve used more than 7 steps to describe your process, then try to either amalgamate several steps into one or break your process out so it spans more than one SIPOC document.
2. Output
The output from the process will be one or more products or services. Examples of outputs include; a manufactured product or part of a product, a report, or a computer file, amongst others.
3. Customer
The customer receives the outputs of the process. The customer could be a person, an organization, or another process.
Customers are important, as it is they who determine if the outputs of a process are satisfactory.
4. Inputs
Inputs are those items which are supplied by the suppliers and are required by the process in order to produce its outputs.
Examples of inputs to a process include spreadsheets, raw materials, data files, emails, signed documents, the output from another process, amongst others.
5. Supplier
A supplier provides one or more inputs to a process.
Suppliers can be internal or external to your organization. Examples of internal suppliers include team members, departments, or other divisions of your organization. Examples of external suppliers include couriers, other companies, government agencies, and external consultants, amongst others.
Customer Focused Process Improvement
When we create a SIPOC document we usually begin by considering the process. However, sometimes the only reason you’ll want to improve a process is to meet the needs of your customer. This is known as being customer-driven, and in this case, it makes sense to begin the process with the customer.
This approach is known as COPIS – Customer, Outputs, Process, Inputs, and Suppliers. COPIS focuses on starting with the end customer in mind. Note that the acronym is simply SIPOC spelled backward.
SIPOC Example
Let’s look at a simple process example that almost office-based managers will be familiar with. Imagine you’re a manager and you’ve just agreed to hire a new employee. You want to ensure that on their start day they have a laptop set up and ready to go so they can hit the ground running.
If this process doesn’t work correctly then your new employee may find they are unable to do any productive work for days, maybe even weeks, while they wait for their new laptop to arrive and be set up.
Here is what the SIPOC example diagram for this process might look like:
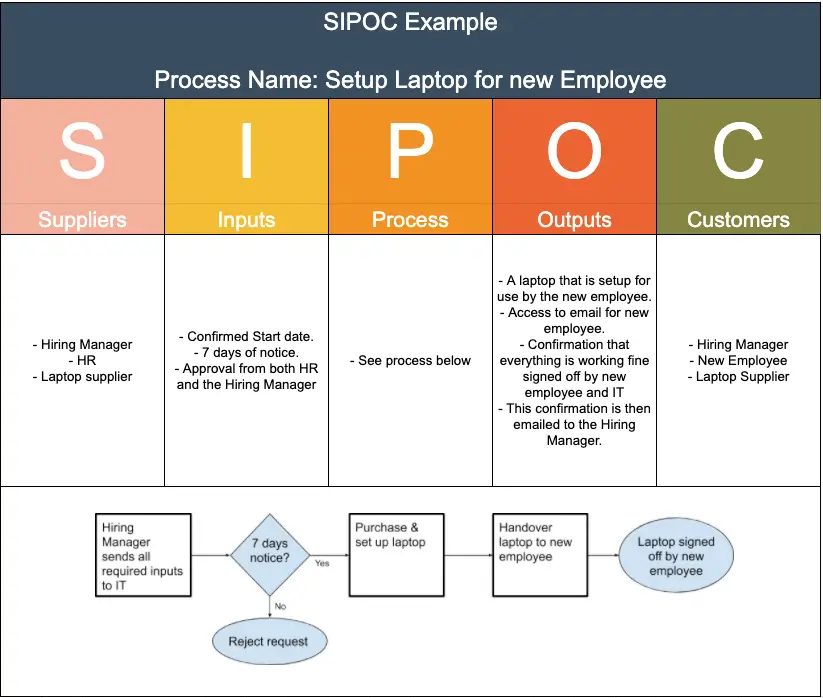
This is a very simple example, but hopefully, you can see that without a process in place that many things could go wrong:
- Communication problems between departments.
- Problems with procurement and delivery.
- A stretched IT team.
- A lack of prioritization.
- A need for an employee onboarding process.
Even with a SIPOC in place, problems might still occur. In this case, it can make sense to zoom in and break down the step causing the problem. For example, you could create a new SIPOC table for the “Purchase & set up laptop” step.
SIPOC Template
We have created a SIPOC Diagram Template in PDF format, which you can use to create your SIPOC diagram. You can download the SIPOC Template PDF here.
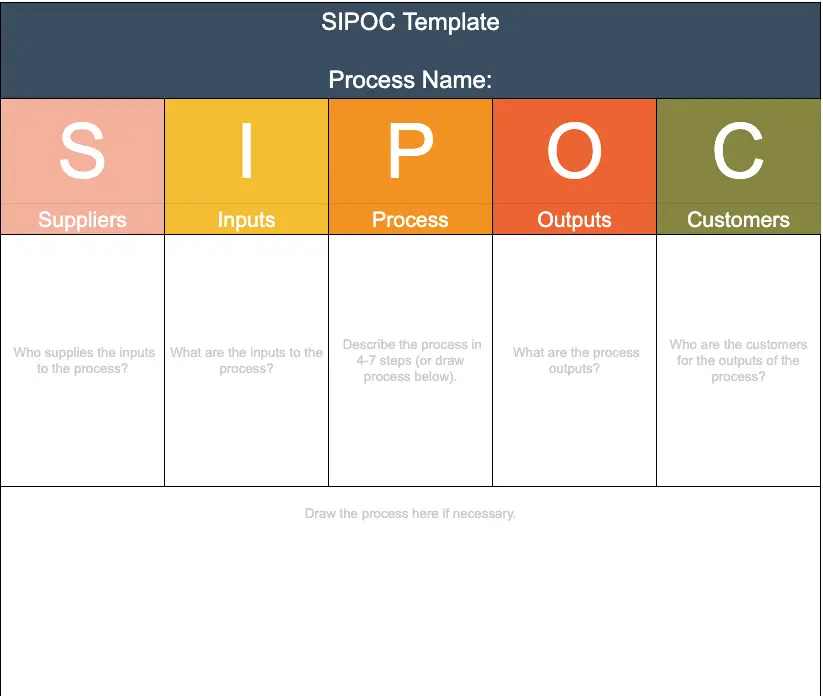
Advantages and Disadvantages
The benefits of the SIPOC model include that it:
- Is easy to understand and use.
- Shows clearly where the process starts and ends.
- Can help you clarify the main steps in a process.
- Ensures your team is aligned in their understanding of a process.
- Makes it easy to understand multiple processes that are chained together.
- Enables you to quickly identify the key inputs and/or outputs of the process.
- Enables you to quickly determine the key suppliers and/or customers of the process.
The disadvantages of the SIPOC model include:
- Using SIPOC alone won’t stop problems occurring within processes.
- It’s very simplistic, so it only serves as a starting point for process mapping.
- Your SIPOC model is only as good as the people who created it. If key people are missing when its created then it’s likely important items will be missing.
Summary
SIPOC is an acronym that stands for Suppliers, Inputs, Process, Outputs, and Customers.
The SIPOC model is suited for mapping a high-level view of a business process. SIPOC provides a way to map a process at a high level, stripping away complexity. This means that the basics of a very complex process can be understood very quickly.